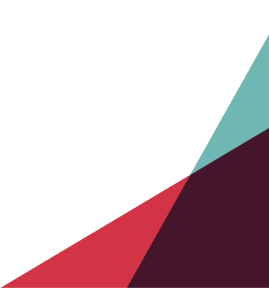
How To Do A Takeoff In Construction – A Step-By-Step Guide
The construction sector has always operated to tight margins, and with building materials prices increasing by 25% in 2022 alone, margins are under greater pressure than ever before.
When producing a bid, general contractors and subcontractors must ensure that projects costs including materials, labour and expenses are accurately estimated. Critical to this is the construction takeoff, the first step in the estimation process.
In this guide, we will look at what a construction takeoff involves and how to complete one effectively to achieve more competitive and profitable bids.
Written by Carol Massay
What Is A Construction Takeoff?
A construction takeoff is the process of counting items or measuring materials based on project blueprints, drawings or models to establish the quantity of materials necessary to complete a job.
Once you list and quantify what’s required, you can start to calculate materials and non-materials costs such as labour. All this information feeds into the estimate and, ultimately, the project bid.
Construction takeoffs should be very accurate and thorough documents, as they are a critical part of the preconstruction process and prepare the ground for commercial success.
Many contractors will also complete their own takeoffs and check these against yours, so a comprehensive, precise approach is important.
Most businesses will be bidding on multiple projects at once and some projects will also be large and complex. Completing takeoffs quickly and efficiently will give you more time to use your analytical skills to produce winning estimates, and increase the number of estimates you are able to complete – all key ingredients to business growth and profitability.
Who Calculates A Takeoff In Construction?
Typically, takeoffs are the responsibility of estimators, who draw on their knowledge and experience from previous projects to ensure bids are both winning and profitable.
In small contracting and subcontracting firms, the task may fall to the owner or a lone estimator, while in big firms, takeoffs are likely to be completed by a team of estimators with specific specialisms such as electrical or structural.
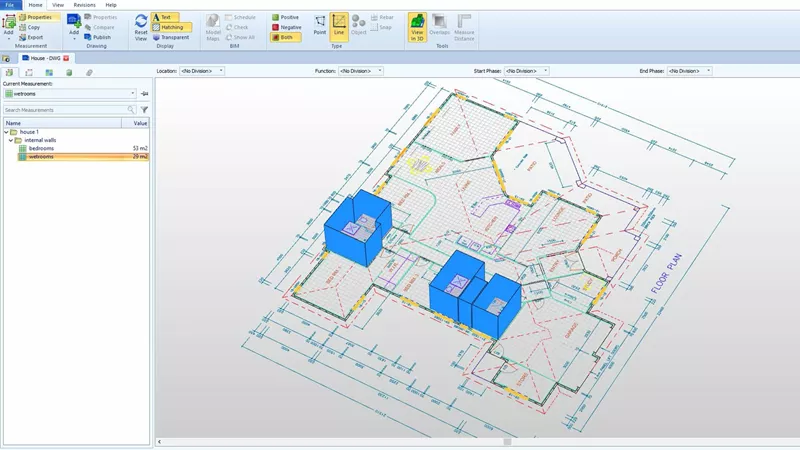
What Are The Different Types Of Takeoff In Construction?
Material and Quantity Takeoff
Material takeoff and quantity takeoff are two closely related terms in construction, but they do have some key differences.
Material takeoff is the process of identifying and quantifying the materials needed to complete a construction project. This includes the type, quantity, and dimensions of the materials. Material takeoff is typically done by reviewing construction plans and specifications.
Quantity takeoff is a more comprehensive process that includes material takeoff alongside other elements of a construction project, such as labor, equipment, and overhead. Quantity takeoff is used to create a detailed estimate of the cost of a construction project.
In other words, material takeoff is focused on the materials needed for a project, while quantity takeoff is focused on the overall cost of the project.
Here is a table that summarises the key differences between material takeoff and quantity takeoff:
|
Material takeoff |
Quantity takeoff |
Focus |
Materials |
Overall cost |
Scope |
Type, quantity, and dimensions of materials |
Materials, labor, equipment, overhead |
Method |
Review of construction plans and specifications |
Review of construction plans and specifications, plus estimating software |
Output |
List of materials and quantities |
Detailed estimate of project cost |
Manual Takeoff
Manual takeoff involves carrying out material counts and measurements by hand using paper blueprints and plans.
It’s not the most efficient way of producing a takeoff. For large or complex projects, manual takeoffs can be particularly laborious.
Plans need to be printed which takes time and costs money. Printed documents also take up space and there is a risk of damage or loss.
Typically, data from manual takeoffs is then entered into spreadsheets or estimating software packages.
The process is time-consuming and prone to human error – this could lead to missed deadlines, inaccuracies or not having the time to produce a carefully considered bid, all of which undermine your business’ growth and profitability.
Digital Takeoff
Digital takeoffs use software packages to streamline and automate the takeoff process, saving time and reducing the likelihood of errors.
There are many advantages to going digital:
- Complete takeoffs faster, allowing more time for producing the estimate
- Increase measurement accuracy
- Reduce manual data entry
- Store documents and plans digitally
- Gain easy access to data from previous projects
Many contractors now supply digital blueprints and plans and Building Information Modelling (BIM) is increasingly becoming a prerequisite for some construction projects, so knowledge of and experience in digital takeoff is an investment in the future of your business.
2D Takeoff
2D takeoff is a type of digital takeoff which uses PDF, CAD and other 2D blueprint and drawings. With a click of the mouse, you can calculate areas, lengths and counts and enter these on spreadsheets or estimating software solutions.
3D Takeoff
Digital 3D takeoff uses 3D models and BIM, though the use of BIM is not widespread yet and it doesn’t always give estimators all the information they need.
3D takeoff speeds up the takeoff process by helping you easily visualise the scope of a project, filter down by systems, access different scale views of the project and quickly see any elements which are missing but should be included in the estimate.
Complete 2D and 3D Takeoff With Access ConQuest
Our construction estimating software, Access ConQuest, includes an on-screen takeoff module which automatically lifts measurements from both 2D and 3D documents and adds them to your Bill of Quantities with a single click. Save time and simplify takeoff with Access ConQuest.
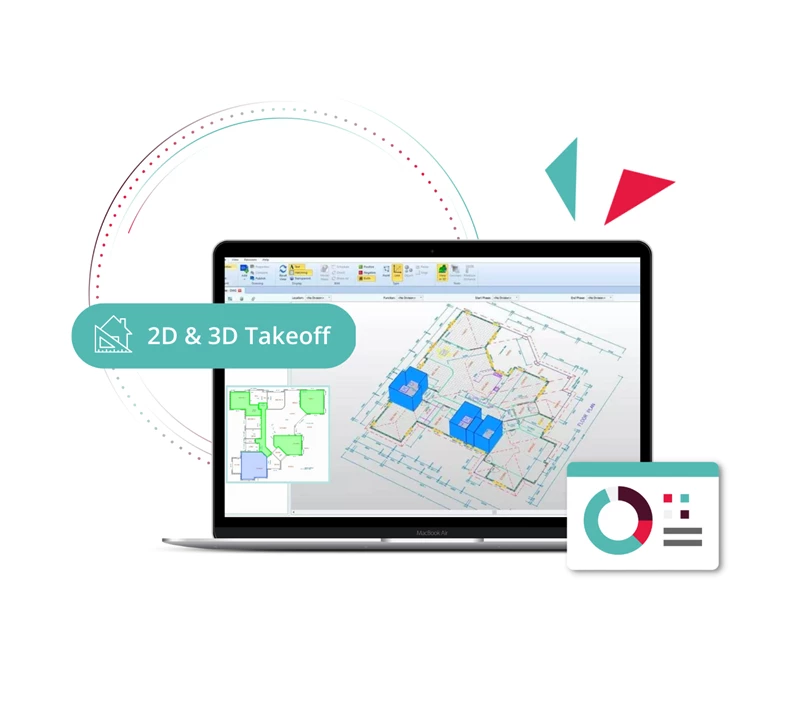
How To Do A Takeoff In Construction – Step-by-Step
- Review your project plans
- List required materials
- Measure project components
- Calculate quantities of your materials
- Create a takeoff sheet
Step One – Review Your Project Plans
This is the most important step in the process, as it will give you a clear understanding of what materials are required for the project.
You should carefully review blueprints, specifications, and any other documentation that is relevant to the project. Pay attention to the details, such as the size, type, and quantity of materials required.
Step Two – List The Required Materials
Once you have a good understanding of the project plans, you can start counting the number of items required. This can be a tedious process which can be automated using takeoff software, but it is important to be as accurate as possible. You should also list the materials in a way that makes sense, such as by type, size, or quantity.
If using takeoff software, it is important to review and modify the counts before moving to the next step.
Step Three – Measure The Project Components
In addition to counting the number of items, you will also need to determine accurate measurements of your project. This is important for determining the quantities of materials required.
For example, if you are building a wall, you will need to measure the length, height, and thickness of the wall.
The process varies greatly between manual and digital takeoff, as manual process will require taking measurements on paper plans using a scale ruler, whereas digital takeoffs help automate this process.
Step Four – Calculate Quantities Of Materials
Once you have counted the number of items and measured the various components, you can determine the quantities of materials required. This is done by multiplying the number of items by their respective measurements. For example, if you are building a wall with 100 bricks, each of which is 12 inches long, you will need 1200 inches of brick.
Step Five – Determine Your Costs
The next step is to determine the costs of the materials. This can be done by researching the current market prices for each material. You can find this information online or by contacting suppliers.
Using construction software can make this step much easier with updated price libraries.
Step Six – Create A Takeoff Sheet
Once you have gathered all of the information, you can create a takeoff sheet. This is a document that summarises all of the information you have gathered in the previous steps. It should include the name of the project, the materials required, the quantities, the costs, and any other relevant information.
Once you have created the takeoff sheet, it's important to review it carefully to make sure that all of the information is accurate. You should also get someone else to review it to catch any errors that you may have missed.
How Can You Improve Your Takeoff?
At the start of this guide we emphasised the importance of accurate takeoffs in the commercial success of bids. We also covered the advantages of digital compared to manual takeoffs. But there are additional ways that you can improve your takeoffs, and ultimately, your bids:
- Historically, 2D and 3D takeoffs involve separate applications. Having software in place which enables the two processes to work together on one platform delivers the most comprehensive outcomes.
- Cloud-based takeoff software offers a single point of storage for the most up to date project documents, drawings, and models, easily accessible to all who need them when they need them. Changes and version control are much easier to manage and collaboration between teams is possible.
- A takeoff solution which integrates with construction estimating software eliminates the need to export or manually enter data into your estimating package, steps which could introduce errors into your process. Creating a Bill of Materials is then a much more seamless, faster process. This connectivity also allows for the analysis of previous projects, to understand profitability and shape business strategy.
Discover how Access takeoff software can boost your margins and increase your bid-to-win ratio
Explore our latest estimating software resources
Read our latest content on all things construction estimating software covering key industry questions and trends.