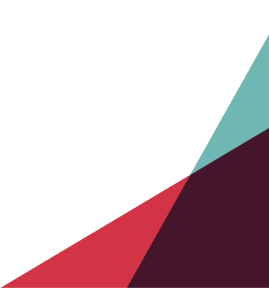
Common Construction Estimating Mistakes and How To Avoid Them
In a recent QuickBooks survey, 30% of construction companies surveyed were not making as much profit as they thought they would and 40% had little confidence in their estimates.
In this article, we review common estimating mistakes to look out for to help you improve accuracy and profitability.

Written by Carol Massay
Why Are Mistakes Common In The Construction Estimating Process?
Estimating is a challenging job. There are many variables to consider when estimating which means many opportunities to make mistakes. Labour and material costs, risk estimation and takeoff measurements must be precise to avoid losing a potentially large amount of money.
The estimating process is prone to mistakes for several reasons, often relating to human error or lack of transparency and collaboration across projects. A few of the most common reasons are:
- All projects are unique, so past knowledge can’t be relied upon.
- Lack of a clear definition of scope of a project.
- Stress to meet time pressures and rushing through the job.
- Temptation to appease the client with a lower estimate.
- Lack of historical data or access to data in general.
- Lack of experience in cost estimation.
- Lack of collaboration with other stakeholders e.g. subcontractors.
- Working on spreadsheets instead of specialised estimating software.
9 Common Construction Estimating Mistakes
1. Not Visiting The Site Before Estimating
Tight deadlines and time pressures often mean that site visits are skipped before making an estimate. Relying solely on prior experience is risky, no two sites are identical.
Visiting a site will ensure that estimators do not make assumptions that lead to costly mistakes. Each site has its own characteristics and visiting allows estimators to gather valuable insights to increase estimating accuracy.
Unknown site conditions can cause unforeseen challenges during construction. Going on site gives the estimator a chance to:
- Take precise measurements
- Inspect topography
- Take soil bore samples
- Check road access
- Check space available for equipment and materials
- See what existing structures need demolishing or altering
- See which environmental protections are needed
- Build rapport with project staff and clients in person
It is also a good idea to involve subcontractors in site visits to fill any knowledge gaps. First-hand knowledge of what might impact on their work will highlight any missed considerations or additional costs.
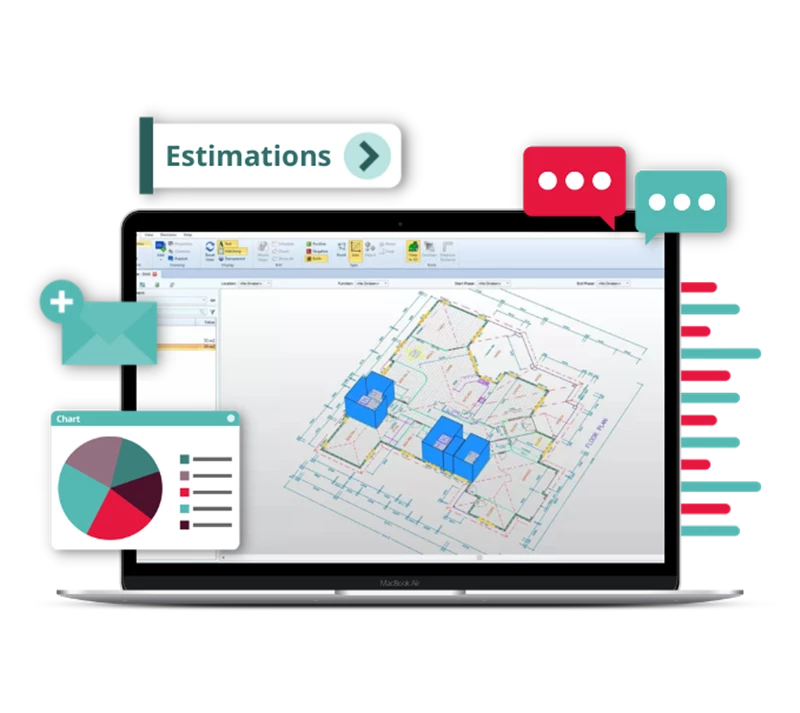
2. Flawed Takeoff
An accurate takeoff lays the foundation for estimates. Inaccurate or incomplete takeoff lists can massively impact an estimate. Takeoffs are required to determine the exact quantities of materials and supplies necessary to complete a project, which informs the labour and equipment needed.
Costs fluctuate significantly between grades of steel or material brands; incorrect specifications can impact labour and equipment. Workers may not have what they need or the experience necessary to complete the job, leading to delays and added costs.
Missing items or inaccurate measurements leads to over- or under-estimating a project. Overestimating might lose a bid; underestimating impacts the success and profitability of a project.
Learn how Access' takeoff software can improve the accuracy of your Takeoffs.
Create Accurate Estimates Every Time With Construction Estimating Software
Access ConQuest is easy-to-use estimating software designed by and for the industry to create accurate estimates, fast. Packed with useful features, estimating teams can work collaboratively on the cloud to build bills of quantities using our price library of over 10 million items.
3. Lack of Transparency and Collaboration
Data transparency across construction projects encourages collaboration between different stages and teams. Collaboration will help to fill any knowledge gaps and highlight any missed considerations when preparing an estimate. Collaborating with the workers that will carry out the tasks in the estimate allows for greater detail in the areas where the estimator’s knowledge falls short. To make estimates transparent, and encourage collaboration there needs to be:
- A high-level overview as well as line-by-line details, so that everyone can understand regardless of experience
- Digital systems in place to help with data sharing and give a single version of the truth
- A culture of collaboration from the very beginning of a project
Read more about the The benefits of collaboration in construction (and how to achieve it) >
4. Underestimating Labour Costs
Labour costs are thought of as the most difficult cost to estimate, and the most expensive.
There are many variables to consider that can sometimes be overlooked, such as overtime, travel, tax, employee benefits, or insurance. Costs for the same task will change depending on the worker hired. An experienced worker will be more expensive but will have higher productivity, and vice versa for an inexperienced worker. It is a balancing act to decide the ratio of productivity to pay.
A common way of cost estimating labour is to determine how many man-hours it will take for each task. Being as detailed as possible and capturing labour information in assemblies will ensure any changes will be reflected in labour costs. Try to calculate cost per square foot and compare historical data from previous similar projects. This level of detail will also inform the source and impact of deviations on project costs and offer well documented data for future projects.
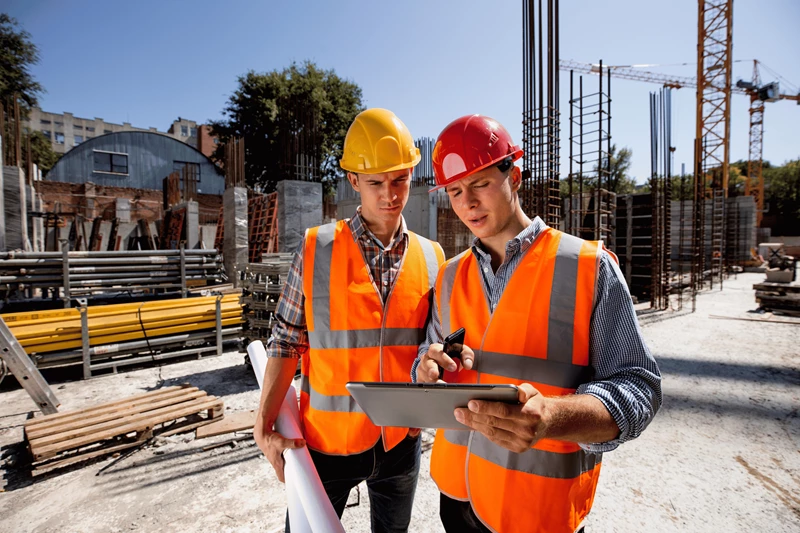
5. Inaccurate Materials and Supplies Costs
Material prices can fluctuate significantly from starting an estimate to starting construction. The demand for materials is high and there is often uncertainty around tariffs. It is crucial to build strong relationships with reliable manufacturers and suppliers to be able to negotiate price locks and give an accurate material estimate. Also, providers need to know the correct quantities for them to fulfil orders and deliver on time. Delays on materials will impact on worker schedules and costs.
6. Limited View During Cost-Estimation Process
Part of the cost-estimation process is breaking down the project into detailed information on the costs associated with each task. Data should be easy to filter down or grouped so that everyone has access to the information they need, for example, data on activities, phase, labour, and classification.
Not only is this valuable data to collect on a project for future comparisons, but it also provides validation for each cost estimate so there is no room for surprises. Having view of all this data makes it easier to pull reports or see the source of any additional or unexpected costs. A high level of detail and customisable views can be difficult to achieve and maintain via spreadsheets and may need specialised estimating software that automatically updates and formats information.
7. Last Minute Changes and Rework
Last minute price changes for materials, fuel or subcontractors are common. Late changes often result in formula errors or missed line items.
Without a standardised estimating process or estimating software, it can be difficult to track changes and source the cause of any issues. Last minute changes using manual methods, such as spreadsheets, can also be very time-consuming and stressful to complete.
Cost estimating software eliminates human error through built-in formulas and price libraries so that costs are updated automatically with any changes. It also standardises estimating processes so that projects can be easily compared.
8. No Risk Estimation
Every construction project has risks. Assessing risk is an integral part of the estimating process and will help to accurately plan and mitigate any potential problems that might arise.
Failing to assess the level of risk can be detrimental to a project’s success and profitability.
Accurately assessing risk can determine whether a project is worth bidding on. The larger the risk the longer the amount of time that needs to be dedicated to estimating costs and analysis. The likelihood of each risk happening needs to be weighed against how badly they could impact the project. Profit loss is likely if an unforeseen issue arises without plans for mitigation or the associated costs accounted for.
Common risks to consider are:
- The project owner’s age, reputation and experience
- Project pricing flexibility
- Type of materials needed
- Are the materials prone to price fluctuations
- Weather and seasonality
Using past project data and risk estimations of similar projects can help determine potential risks that may have been overlooked.
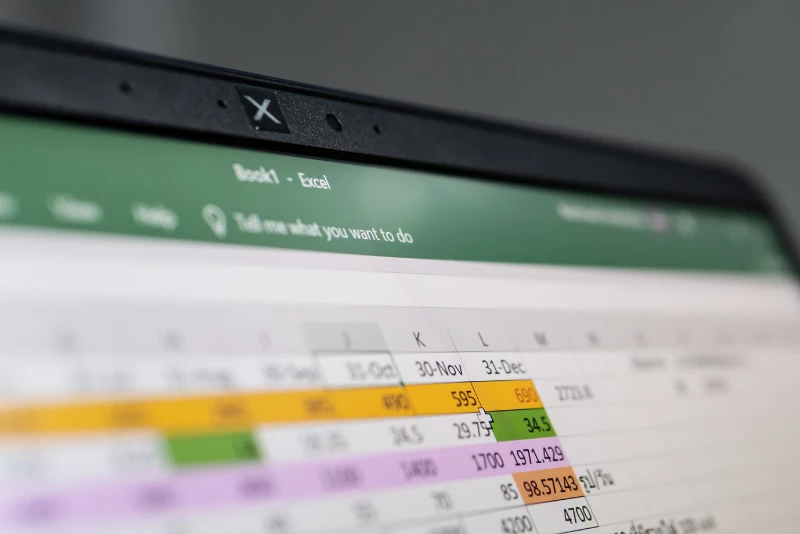
9. Building Estimates On Excel
Compiling estimates on Excel spreadsheets leaves a lot of opportunity for human error. Spreadsheets are very manual and time-consuming to set up, often leading to people cutting corners to meet deadlines and omitting valuable information. With many people contributing to an estimate, and with Excel not having a standardised construction estimating template to follow, legacy spreadsheets grow and change leading to major rework and in-built mistakes.
Collaboration becomes difficult without a central system to work from, and no audit trail allows for changes to be lost. Edits may happen to a version of the estimate but not the core version, resulting in miscommunication and missed information.
Cloud-based construction estimating software ensures that data is updated in real-time so that everyone can access and view the same estimate. Collaborating across teams becomes much more productive and estimates are completed much faster. Storing data in the cloud not only protects the data but allows for it to be accessed when completing estimates for future projects.
Read our Excel Vs Construction Estimating Software article to get an overview of both solutions.
Discover how Access Conquest can boost your margins and increase your bid-to-win ratio
Explore our latest estimating software resources
Read our latest content on all things construction estimating software covering key industry questions and trends.