Free MRP Software vs Excel vs Paid MRP Software
When it comes to material requirements planning (MRP) software, businesses often face a decision: should they invest in a paid MRP solution or stick with free MRP software? This comparison will guide you through the pros and cons of both options, helping you decide which is best for your business. We’ll also explore the use of Excel as a manual alternative to MRP software, highlighting the key differences between using Excel vs MRP systems.
What is Free MRP Software?
Free MRP software refers to open-source or limited-feature versions of MRP solutions. They provide basic functionality for inventory control, production planning, and order management but often come with limitations. There are different types of free MRP software models:
- Freemium: Basic features are free, but advanced functionalities come at a cost.
- Trial versions: Some offer a free trial, like Katana's 14-day access.
- Open source: These versions allow for customisation, but you may need a developer to maintain and modify them.
- Excel-based solutions: Some businesses create MRP spreadsheets using Excel. Although accessible,
- Excel has its drawbacks—manual updates, scalability issues, and lack of automation.
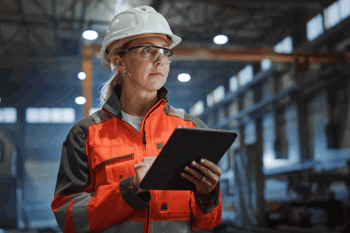
What Can Free MRP Software Do?
For small businesses or startups with less complex requirements, free MRP software offers a good starting point, allowing you to manage:
- Production scheduling
- Stock control (raw materials, WIP, finished goods)
- Bill of Materials (BoM) management
- Supplier management
- Machine downtime tracking
However, more complex functionalities or additional features—like hosting, advanced reporting, or dedicated customer support—often come with added costs.
Free MRP Software Options
Several free MRP software options are available that provide basic functionalities. Here’s a brief comparison of some popular choices:
MRPeasy
Pros: Offers core features like BoM, production scheduling, and inventory management.
Cons: Requires in-house development to customise the open-source version, and costs rise with additional users.
Odoo MRP
Pros: A cloud-based solution with modules for inventory, billing, and manufacturing.
Cons: Lacks the specialised features needed by complex manufacturers and may require further purchases to access full functionality.
Excel
Pros: Widely available, allows for tracking of production plans, and raw materials.
Cons: Files can become large and error-prone; MRP in Excel is a stopgap solution for growing businesses.
Pros and Cons of Free MRP Software
Pros:
- Cost-effective: The obvious benefit is no upfront licensing fees or subscription costs.
- Customisation: Open-source MRP allows for tailored modifications.
- Scalability for small businesses: A good starting point if you have simpler manufacturing needs.
Cons:
- Limited features: Freemium versions or trials often restrict access to more advanced functionalities.
- Scalability concerns: Free solutions may not support growing businesses or complex operations.
- Manual work: Open-source solutions may require a skilled IT team to customise and maintain.
Comparing Excel with Paid MRP Software
Many smaller businesses start with Excel-based MRP systems because it’s a tool they already know. However, as businesses grow, Excel can become cumbersome and may not provide the level of automation or real-time insights needed to scale efficiently.
Pros of Using Excel:
- Cost-effective: There's no software to purchase if you already have Excel.
- Familiarity: Most people are already familiar with how to use Excel, reducing the need for extensive training.
- Customisation: You can tailor your Excel MRP template to meet your specific needs.
Cons of Using Excel:
- Manual input and errors: Excel requires manual data entry, increasing the risk of errors and inefficiency.
- Scalability issues: As your business grows, maintaining complex spreadsheets can become a burden.
- Lack of automation: Excel doesn’t offer the automated processes that MRP systems provide, such as real-time updates or production scheduling.
When Should You Choose Paid MRP Software?
While free MRP options may work for small-scale operations, businesses with more complex requirements often benefit from paid MRP software. These systems are built to handle greater volumes of data, more complex workflows, and integrate seamlessly with other tools like CRM or financial systems. Paid MRP systems offer:
- Comprehensive features: From inventory management to real-time tracking and advanced reporting.
- Customer support and training: Dedicated assistance to help with implementation and usage.
- Scalability: Paid solutions grow with your business, providing flexibility as you expand.
- Automated updates and maintenance: Regular software updates without manual intervention.
Which is Right for You?
If you’re a small business or startup with very basic material resource planning needs, Excel may be a cost-effective option. It's easy to use, familiar to most, and allows you to test simple MRP processes without committing to any specific provider. Free MRP software, particularly open-source options, can also be a great starting point.
For mid-market organisations and larger manufacturing companies, free MRP software or Excel might become impractical as your business grows. The lack of advanced capabilities, automation, and support in these solutions can hinder your ability to scale efficiently and manage complex processes.
This makes paid MRP software a worthwhile investment, offering comprehensive features, better support, and long-term scalability. Paid solutions are more robust, offer seamless integration with other business systems, and reduce the risk of errors or inefficiencies, making them the best choice for businesses with more complex manufacturing and operational needs.
Why choose our paid MRP software?
With Access FactoryMaster MRP software, you can import your sales orders and automatically generate purchase orders for raw material or components. FactoryMaster takes into account variables such as purchase orders, work in progress, delivery commitments, stock levels and purchase lead times.
It gives you full visibility of your operation (including shop floor data capture) and unbeatable traceability, giving you control over your cash flow and opportunity for growth.