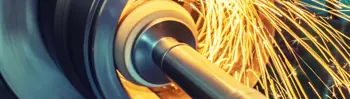
ERP vs APS Key Summary
Feature |
ERP (Enterprise Resource Planning) |
APS (Advanced Planning and Scheduling) |
Main Purpose |
Manages overall business functions: inventory, finance, sales |
Optimises production schedule based on real-time data |
Strengths |
Centralises data, supports high-level decision-making |
Precision scheduling, real-time adjustments |
Weaknesses |
Slow to adapt, lacks scheduling flexibility |
Requires ERP data, high maintenance, complex to set up |
Ideal For |
Big-picture management, data consolidation |
Detailed, constraint-based scheduling |
Real-Time Scenario Planning |
Limited, difficult to configure |
Built-in, handles multiple “what-if” scenarios |
Ease of Integration |
Complex when paired with APS; syncing issues can occur |
Requires ERP data; integration setup can be challenging |
Best Suited For |
Businesses needing a unified data hub |
Manufacturers with dynamic, complex production needs |
ERP - the "Jack of All Trades"
ERP systems are the backbone of any manufacturing setup that wants a single source of truth across departments. Systems are designed to keep everyone in a business on the same page by standardising processes, collecting essential data, and delivering the right information to the right people at the right time.
At the management level, ERP provides real-time data and business intelligence, enabling leaders to make informed, data-driven decisions both for daily operations and for longer-term planning.
From sales forecasts and cash flow to profitability analysis and traceability, ERP consolidates all key information, streamlining access and reducing the need for complex tracking and reporting systems.
The Bottom Line on ERP: Great for managing the basics, but can sometimes struggle to handle the nitty-gritty of your daily scheduling needs.
APS - the Optimiser
APS software is designed to do what ERP can't. That is, to create a precise, efficient production schedule that reflects your actual capacity, constraints, and real-time changes. It works with data from your ERP system—like BoMs, routings, and MRP—to allocate time slots for each step of production, ensuring the right equipment, labour, and materials are applied.
When things change—whether it's a last-minute order or an equipment breakdown—APS quickly recalculates the impact and adjusts the plan accordingly. This allows you to optimise production at a granular level, adjusting schedules on the fly to maximise efficiency.
However, APS isn't a plug-and-play solution. It requires careful configuration, ongoing updates, and relies heavily on your ERP data to provide accurate results. It’s not a “set-it-and-forget-it” tool—getting the most out of APS means being prepared for a learning curve and continuous maintenance.
The Bottom Line on APS: APS offers powerful scheduling capabilities that improve efficiency and profitability, but it requires investment in setup and upkeep to deliver on its potential.
Find out more about what advanced planning and scheduling is.
Using ERP + APS Together
If you’ve already invested in an ERP system, adding production scheduling software can give you a much-needed edge.
Some ERP systems include Gantt charts for planning and scheduling, but they are difficult to configure and lack the granularity of an APS system. ERP systems often struggle with scenario analysis due to their complexity, requiring the creation of hypothetical resources in a live system. In contrast, APS systems enable scenario analysis, allowing management to make data-driven decisions based on realistic outcomes.
APS allows for "what if" scenarios to analyse the impact of changes like job reordering or delays. It also supports real-time adjustments for issues like equipment breakdowns, operator absences, or shifting client demands. This flexibility helps manufacturing and planning teams optimise production schedules at a granular level, improving efficiency and driving incremental gains.
For businesses looking to scale, APS provides insights into capacity, bottlenecks, and areas where investment is needed to increase throughput. In competitive industries with complex operations, investing in an effective planning system upfront is critical to meeting demanding OTIF targets and staying ahead of the competition.
The Bottom Line on Using both ERP and APS together: It enables seamless operational management and detailed, real-time planning optimisation, driving efficiency and better decision-making across the business.
Find out more about our ERP system.