Material Requirements Planning (MRP)
- Easily create orders for process or batch manufacturing, while being able to take into account the existing lead times.
- Use the Control Desk feature for rapid creations of suggested purchase and works orders, and use MRP functionality to make suggestions on purchased orders that should be cancelled or rescheduled.
- The system calculates requirements for finished batches and links back to your purchase order schedule.
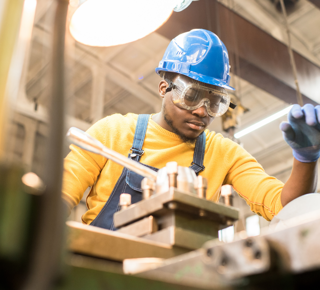