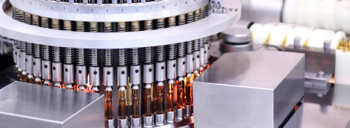
The process - a study in complexity
Biopharmaceutical vaccine production is characterised by complex processes involving a large number of intermediate solutions. In this instance, there is an added dimension of multiple trains operating simultaneously, many of which share resources. Multiple stages and multiple products vying for the same space in the manufacturing suite. It involves hundreds of discrete activities to be performed, solutions to be made and cleans to be carried out on bioreactors, columns and filtration systems, all in a 24/7 environment that involves 200 people. The manufacturing plant is hard piped, so everything has to be finely synchronised to work optimally.
From spreadsheets…
The ‘morning production meeting’ had previously been dominated by Excel spreadsheets prepared and maintained by four full-time planners for one product set and a further three for the second. Each had an intimate knowledge of specific parts of the production process, involving many hundreds of discrete solutions and activities. Because of the complexity, the rolling plan could cover only a week ahead, updated daily to accommodate all the unforeseen events that had happened in the previous 24 hours. The process was laborious, taking a whole morning each day, the separate plans
lacked detail and engineering had to be planned informally between planners and engineers. It was not uncommon for electrical engineers, mechanical engineers and equipment to turn up for planned maintenance, only to learn that the schedule had changed and production was in process.
…to automation and full visibility
Having installed Orchestrate, the process is so much smoother and more effective. Using fewer schedulers, the daily rolling plan now covers a four week period, rather than one, and takes only an hour to complete, instead of a morning.
"Particularly important, communications have been revolutionised. Everyone in the facility has access to the plan from shift managers and supervisors to shift engineers and engineering planners. Giant touch-screen smart boards are sited on the floor and user screens provide access around the plant. A real-time ‘single version of the truth’ available to everyone, in an environment where processes take place in multiple rooms. A major benefit from improved communications has been significantly smoother shift changeovers."
A senior planner describes the improvements to engineering planning:
"Where maintenance had previously been performed as an ‘add on’, it is now fully integrated. Maintenance activities determined within our ERP system are now fed into Orchestrate, which schedules (and more importantly re-schedules in light of unplanned changes) maintenance tasks into non-production slots. The same is true for calibration of equipment and unplanned requests for downtime. Everyone informed."
Implementation was smooth too. Recognising that most people are resistant to change, the Orchestrate plan is displayed in much the same way as the old Excel spreadsheets, except it is now possible to burrow down into detail. A six week parallel run was planned to accommodate the change from old to new but, in practice, reactions from users were so positive, the parallel run was dropped after just a few days.
The last word comes from the plant director responsible for vaccine production:
“For me, visibility is the biggest single win; everyone having access, whatever level of detail they need. That alone fully justifies the system.”