Warehouse receiving: Streamlining processes for optimal efficiency
3PL (third-party logistics) providers now play a critical role in the supply chain, helping retailers service ever-increasing customer orders and expectations. But with these surging demands comes an increased pressure for 3PLs to enhance logistics effectiveness. And the key to doing so? By embracing new innovative ways of doing business – an imperative recognised by 71 per cent of 3PL partners and 91 per cent of 3PLs.1
Warehouse management systems offers the innovation 3PLs need, helping them deliver faster, more efficient services, at scale. So, what revolutionary forms of technology are helping 3PLs save time, reduce costs and meet the surging demands of retailers? This guide will provide all you need to know by delving into the following:
- What is the warehouse technology of tomorrow?
- Top 3 wareho
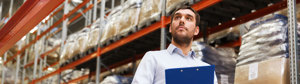
Understanding the warehouse receiving process
The warehouse receiving process is the critical first step in fulfilling customer orders, encompassing the delivery, unloading and storage of warehouse inventory. In short, it is the process of restocking ecommerce inventory in a warehouse or fulfillment centre.
A comprehensive, clearly defined warehouse receiving process plays a central role in ensuring inventory management and fulfillment run as as smoothly and cost-efficiently as possible.
Exploring the stages of the warehouse receiving process
Receiving the right goods, in the right quantity and at the right time, is the primary objective of the warehouse receiving process. Achieving this may sound simple, but to ensure error-free warehouse receiving, a clearly defined and strategic process is required.
Below, we detail the five vital stages of a best-practice warehouse receiving process:
- Provide the right documentation to suppliers
Clear communication with your suppliers is key to minimising warehouse receiving errors and enhancing efficiency. This means that prior to ordering goods, you must send your suppliers proper documentation that outlines your packaging requirements.
Essential information to include in your documentation includes:
- Where labels must be positioned and what information they must contain
- If the goods must be placed on pallets or if they are loose cargo
- The quantity of items per container or carton
- The quantity of packages per pallet
- The acceptable size and weight of packages
With the right warehouse management software, you can dramatically simplify the process of checking that you received the right cargo from a supplier. All it takes is to simply scan the barcode on the Warehouse Receiving Order label (WRO), and all the details of your order are displayed instantly.
- Receive and unload stock
This step is all about having the right procedures in place to ensure warehouse personnel receive and unload your shipment as efficiently as possible.
Essential to achieving this is for personnel to meet the supplier at the loading dock, and prior to doing so, ensuring the truck beds are packed back-to-front in reverse delivery order. This allows for the immediate unloading of goods without needing to first move other items. Heavy lifting machinery like a forklift may be required.
To minimise errors, it is vital that warehouse personnel are sufficiently trained in the handling and receiving process. If they notice any concerns with delivered cargo, personnel should immediately raise them with the cargo provider prior to signing the delivery notice.
- Count and inspect stock
After receiving the cargo, it is vital for warehouse personnel to conduct a thorough inspection. This includes checking the quantity of goods received, their condition, the integrity of seals and product codes. The products received must also be cross-checked with those listed on the WRO.
Any discrepancies between what was ordered and what was received must be raised with the supplier as soon as possible. While any damaged goods must be put aside so that they can be returned to the supplier.
- Store stock
The last step in the warehouse receiving process is to organise and store the cargo in the warehouse. Depending on their size and weight, products can be stored on shelves, pallets or in bins.
Where many businesses get warehouse receiving wrong
For many businesses, mishandling of the warehouse receiving process comes down to one issue – a lack of established procedures and a checklist. Without these to guide warehouse staff, inaccurate or lost inventory becomes a very real possibility. So too the potentially disastrous scenario of customers ordering stock that is not actually at the warehouse.
This is why it is so critical for businesses to provide warehouse personnel with clear, step-by-step guidance on how to unload, check and store inventory. They must be made aware of established processes, what questions to ask and details to check.
4 ways to optimise your warehouse receiving process
So, how can you not only avoid common warehouse receiving pitfalls, but also enhance your process for maximum efficiency and accuracy? Here are four best-practice tips.
- Save time with warehouse management software
Leveraging the powerful automation of cloud software is one of the easiest ways to simplify the warehouse receiving process.
Ecommerce businesses, 3PLs and fulfilment partners worldwide are increasingly turning to a warehouse management system to automate a range of tasks – from tracking inventory levels and reordering stock, to calculating optimal storage layouts and shipping goods out to customers.
But streamlined processes are only half of the reason behind the rapid adoption of warehouse management software. It also provides warehouse operators with real-time visibility of inventory – when an item is scanned, they can immediately see inventory numbers change.
- Keep track of relevant warehouse metrics
When your warehouse is guided by established procedures for receiving stock, tracking inventory levels and logistics costs becomes far simpler – particularly if you need to do so across several warehouses or fulfilment centres.
Again, this is where warehouse management software can help you gain powerful insights into your warehouse operations. Via intuitive dashboards, you can easily track productivity metrics, all from one place.
- Perform regular inventory inspections
Performing a thorough check of received goods not only helps ensure you get what you ordered, but also prevent the delivery of damaged goods to customers. It is ideal to conduct this check when goods are received, so you can quickly notify the supplier about any damaged, incorrect or missing items.
This ideal scenario, however, is not always possible. It is therefore wise to perform regular inventory audits, including physical counts and cutoff analyses, to ensure any issues or inventory imbalances do not go unnoticed.
- Implement a system for checking documentation
An efficient and error-free warehouse receiving process means that when it comes to documentation, you need to dot all your i’s and cross all your t’s. Comparing your receiving inventory against your purchase order, and spotting any discrepancies early, will save significant time and money.
The best way to ensure that all your receiving and shipping documents are organised and accessible is to create a system. Numbering and labelling documents in sequential order will make double-checking paperwork and spotting missing inventory far simpler for warehouse personnel.
Top 3 reasons to optimise your warehouse receiving process
The primary goal of an optimised warehouse receiving process is to ensure you have the right products, in the right condition and quantity, available and ready to ship to customers. It can help your business:
- Boost stock count precision
Inaccurate stock counts can spell disaster for your fulfilment operation. It can mean that you may have less stock on hand than you think, and lead to customers ordering a product that is not actually in your warehouse.
A comprehensive warehouse receiving checklist helps you avoid this nightmare scenario. And even more so, the powerful automation offered by warehouse management software. By simply scanning inventory, it can provide you with real-time visibility of stock levels, ensuring every delivery matches the original order.
- Minimise understocking and overstocking
The consequences of stock shortages can be disastrous for your business. Failing to deliver what customers ordered can seriously harm your reputation, and it is the quickest way to send your business to the competition.
An overstocked warehouse, on the other hand, means that not only is dead stock occupying valuable space, but in its idle state it is failing to deliver a return on investment.
By implementing an optimised warehouse receiving process, you can avoid these problems by ensuring that suppliers deliver the right stock, in the right quantity, at the right time.
- Optimise inventory storage
Enhancing your warehouse receiving process can also help ensure that stock is stored in the most optimal way possible, reducing costs and saving you time. Warehouse management software, provides the quickest way to do this.
By scanning a product, staff can instantly access instructions on the best way to unpack and store items. And when the time comes to send items to customers, it can instruct them on the best way to pick, pack and ship items.
How Access Mintsoft can enhance your warehouse receiving procedure
Offering powerful automation capabilities, Access Mintsoft makes it simple to optimise your warehouse receiving process, ensuring that it is as efficient as possible.
This easy-to-use cloud solution automates the process of counting, checking and organising stock, while providing real-time visibility of inventory levels, picking rates and shipments. Plus, its advanced reporting capabilities deliver the data-driven insights you need to identify areas improvement, so you can save time and reduce costs.
Book a demo or download a brochure to discover how you can achieve a smoother, more cost-efficient receiving process with Access Mintsoft.