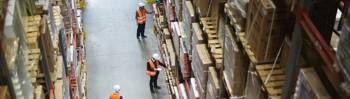
Understanding warehouse picking and packing
The picking and packing process can have an outsized effect on your business’s profitability and reputation. If error-prone and inefficient, you will likely struggle to get orders out with the speed and accuracy required to ensure happy customers.
The last thing you need is to deal with returns caused by incorrectly picked orders or with negative reviews due to late deliveries. That is why it is so critical to plan or review your picking and packing process to identify areas for improvement and ensure maximum efficiency.
In this guide, you will learn about the picking and packing strategies most commonly used by ecommerce businesses as well as tips to help optimise your operations. Read on to discover:
The basics of picking and packing
Why optimising picking and packing is so critical
The 4 most common picking and packing strategies
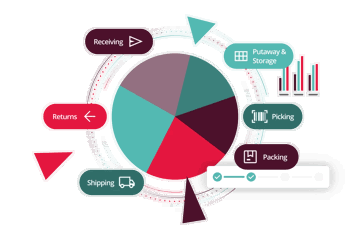
Picking and packing defined
Let’s start by first defining what we mean by picking and packing. In short, picking involves retrieving items from warehouse shelves, while packing is the process of placing the items in a parcel and preparing it for shipping to the customer.
While picking and packing involves a simple process, it is one of the most demanding on warehouse teams. It requires staff to walk considerable distances each day retrieving and lifting often heavy items. All this manual labour influences your bottom line too. Research reveals that picking and packing accounts for up to 70 per cent of warehouse costs.
Why an optimised pick and pack process is critical
Given the costs involved with picking and packing, doing all you can to make the process more efficient and eliminate unnecessary manual tasks will help significantly boost your business’s cost-efficiency. But the need to optimise your processes goes beyond simply cost control.
If you are not doing all you can to optimise your picking and packing, and it lags behind that of your competitors, it is likely you will not be able to match the speed and accuracy with which they service customers. This matters immensely given that today’s online customer holds more power than ever before. Receiving an order late or with incorrect items is enough to see them make their next purchase with the competition.
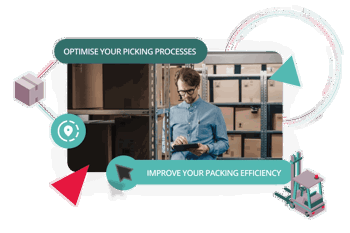
4 picking and packing strategies
The right picking and packing strategy for your ecommerce business will come down to your order volumes, the size of your warehouse and the items you hold. Here, we explore the four most common strategies:
1. Discrete picking
Discrete picking, otherwise known as piece picking or single order picking, is a strategy most commonly used by smaller ecommerce outfits. It entails a single picker or multiple pickers retrieving items and packing them one order at a time.
The advantage of discrete picking is that it is simple to train workers and there is less risk of picking the wrong items compared to more complex picking strategies. The downside, however, is that discrete picking becomes increasingly less efficient as your order volumes grow.
2. Multi-order picking
Multi-order picking, otherwise known as batch picking or batching, reduces the time workers spend travelling through the warehouse to retrieve items. It involves grouping multiple orders into batches. A picker then picks items for the batch of orders at the same time, which means they do not have to repeatedly walk back and forth to the same picking location.
This strategy works well if the orders in the batch contain the same item or a small range of items, and if your business is beginning to receive a higher volume of orders. An order management system helps make multi-order picking easy by identifying which orders to group together and outlining the most efficient picking routes.
3. Zone picking
Zone picking, otherwise known as pick and pass, is ideal if your business has a sizeable warehouse and more than a few pickers. It involves organising your warehouse into several discrete zones and assigning pickers to each zone. Workers then pick multiple items for several orders from their assigned zones. Pickers may pick from their zones simultaneously or one picker may retrieve items from their zone, then pass the order to another picker who will begin retrieving items from their zone.
The main advantage of zone picking is that it cuts down the distance pickers need to walk, however it does require more coordination than the previous picking strategies. This is where an essential warehouse management system can help to ensure no mistakes are made and to easily coordinate picking in multiple zones.
4. Cluster picking
Best suited for ecommerce businesses with a large volume of orders, cluster picking, otherwise known as wave picking, involves picking groups of orders during scheduled times throughout the day. Orders are clustered into a group based on their similar contents and their items are picked within a specific time frame. This can help coordinate the preparation of orders so they can be dispatched at the same time.
Cluster picking can involve using one or more of the picking strategies we discussed previously, and given its complexity, it will need to be managed with the help of a warehouse management system. The system can determine which orders to cluster together and notify staff to start picking them at the same time.
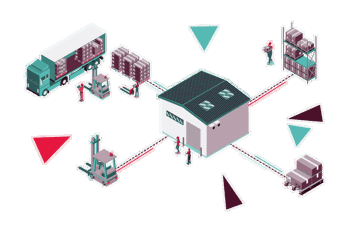
4 ways to enhance picking and packing
Now that you understand the most common picking strategies for ecommerce businesses, how can you ensure they are employed in the most efficient way possible? Here, we detail four tips that can help:
1. Group high-demand items together
If certain items are being ordered at a high rate, either separately or together, it is a good idea to group them together. And not only that, to place them closer to packing and shipping zones. This will help cut down the distance pickers need to travel to retrieve items. It is a good idea to ensure this fast-moving item zone provides sufficient space for multiple pickers to pass through easily.
2. Increase accuracy with barcode scanning
Barcode scanning can help enhance the speed and accuracy of the picking process. When combined with a warehouse management system, pickers can even receive voice-assisted picking commands and view product images to ensure they do not retrieve the wrong items. The software can also suggest optimal picking routes for each picker.
Each item scanned is instantly updated in the warehouse management system, which provides up-to-date visibility of what was picked and what inventory you have on hand. Barcode scanning is one of the most effective ways to boost picking accuracy, often ensuring up to 100 per cent accuracy.
3. Optimise picking routes
Organising your warehouse to minimise the distance pickers need to travel will significantly reduce picking and packing times. This means having a logical flow between different areas for receiving stock, storage, picking, sorting, packing and delivery preparation. This will ensure workers do not have to perform a later process on the way to an earlier one.
It is also important to optimise each section of your warehouse so that the tasks of the next section are made easier. For instance, workers tasked with receiving stock should store stock in a way that makes access easier for pickers. Adequate space between aisles must also be considered to ensure multiple pickers and equipment can easily pass through.
4. Establish KPIs
Setting key metrics by which you can assess picking and packing performance is critical to spot inefficiencies and improve processes. Key metrics can include the cost of labour, picker travel times, the rate at which orders are picked and picking accuracy.
5. Automate and optimise with a WMS
A warehouse management system can help you coordinate strategies like zone and cluster picking, provide real-time visibility of your stock as it moves through your warehouse, and automate manual picking and packing tasks.
It can also make tracking orders across multiple sales channels far simpler for warehouse staff, integrating everything in a single platform. Plus, it can automatically select the most cost-effective couriers and reorder stock when levels become low.
Utilising the automation offered by essential WMS warehouse management software will become ever more critical to deliver the next or same-day delivery customers demand and outperform the competition.
Optimise your warehouse order packing with Access Mintsoft
Our cloud-based warehouse management solution Access Mintsoft offers several features designed to enhance the picking and packing process. The platform intelligently consolidates orders from multiple online shopping platforms, streamlining the picking process and ensuring that the right products are selected for each order.
Access Mintsoft provides real-time visibility into inventory management, including levels and order statuses, allowing a warehouse picker and packer to prioritise tasks based on urgency and demand. It can also help you optimise picking routes and easily coordinate strategies like zone picking or cluster picking.
Trusted by over 600 leading businesses worldwide, Access Mintsoft not only brings automation and efficiency to your picking and packing, but to every aspect of your workflow. The solution streamlines the process of generating shipping labels, creating order/customer documentation and invoicing clients. While advanced data analytics capabilities make tracking sales volumes, inventory and work rates a breeze.
Contact us today to book a demo or discuss how Access Mintsoft can help your business.
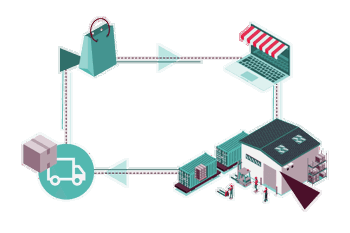
Frequently asked questions
What is warehouse picking?
Warehouse picking is a critical aspect of order fulfilment that entails retrieving specific items from their storage locations so orders can be packed and delivered to the customer
What is a picking list?
A picking list is a document used in warehouse operations to detail items and quantities required to fulfill customer orders. It provides information like item codes, descriptions and their location in the warehouse. Picking lists can be generated manually or electronically via a warehouse management system.
Warehouse personnel use these lists to locate and pick items from inventory. Once picked, items are sent to packing for consolidation and shipment.
What is warehouse packing?
Warehouse packing refers to the process of preparing items for shipment after they have been picked from inventory. It involves carefully arranging products into suitable packaging, such as boxes or parcels and applying the correct shipping label.
How can you improve picking and packing?
Four key strategies to improve the picking and packing process include:
- Using automation and technology, such as barcode scanning systems, to mitigate errors and enhance accuracy during picking tasks.
- Strategically storing frequently ordered items closer to the packing station, allowing for quicker retrieval.
- Establishing the most efficient routes for pickers to reduce the distance they need to cover.
- Using a warehouse management system to automate and coordinate various picking tasks and methods, like batch or wave picking.
What are the three main picking systems?
The three main picking systems are multi-order picking, zone picking and cluster picking. The ideal picking system will depend on the size of the warehouse and volume of orders.