Top 5 warehousing trends to look out for in 2024
Warehouses worldwide are reaping the benefits of the quantum leap in technology we have seen in the last few years. So, what warehouse trends can we expect to take off in 2024 and beyond?
From exoskeletons that help workers with heavy lifting to autonomous robots and predictive AI, we share the fast-growing warehouse management trends in 2024 that make operations more efficient, safer, and greener.
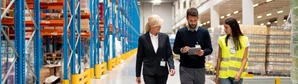
1. Increased adoption of wearables
Warehouse wearables explained
Wearable technology (or wearables) is transforming the way businesses operate – from healthcare providers to retailers and manufacturers. Warehouse operations, too, are fast finding new efficiencies and insights with the help of wearables like glove or wrist scanners, AR (augmented reality) headsets and smart glasses, voice-recognition headsets and exoskeletons.
A 2023 global study revealed that over half (56 per cent) of warehouse and logistics executives are using wearables to boost efficiency, while 42 per cent are set to adopt them in the coming five years.
How do wearables benefit warehouses?
Wearables offer warehouses and their staff two broad benefits – improved health and safety, and enhanced picking efficiency. Let’s take a deeper look at both benefits.
Improved health and safety
One of the most fascinating innovations when it comes to warehouse wearables are exoskeletons, which are full-body, lightweight and battery-powered suits that help workers with heavy lifting. Exoskeletons provide additional support for the back to prevent injuries and repetitive stress to the spine.
Another wearable that improves health and safety are smart glasses and AR headsets. These devices can provide workers with visual instructions that minimise overexertion or awkward movements that may risk injury.
Enhanced picking efficiency
The visual cues provided by smart glasses and AR headsets not only improve health and safety, but also help workers benefit from “vision picking.” That is, picking orders via real-time information in their field of vision, thereby avoiding the need to constantly look down at a device or pick list.
Workers can also scan item barcodes via the camera in the glasses or headset, plus they can also receive verbal instructions and issue their own voice commands. Meanwhile, glove and wrist scanners help warehouse staff work faster by eliminating the need to carry around a scanner.
2. The growing imperative of green warehousing
What is green warehousing?
As with many other sectors, the fulfillment and logistics industries are facing the imperative to do more to minimise their carbon footprint. A growing number of businesses are embracing green warehousing, the idea that warehouses prioritise sustainable practices to minimise their energy consumption, waste, and ecological impact.
Studies show that warehouses contribute 11 per cent of the total greenhouse gasses produced by the global logistics industry. Green warehousing can not only help reduce this figure but also improve the bottom line of businesses that adopt the idea.
A 2023 survey of Australian online shoppers revealed that almost half (47 per cent) preferred to purchase from brands that are known for their sustainable practices. A similar study by Monash University found that over half (51 per cent) of Australian shoppers consider sustainability a critical factor when buying goods.
How can businesses embrace green warehousing?
Forward-thinking warehouses worldwide are fast adopting a range of strategies to reduce their environmental impact. Here, we detail the most effective:
Energy-efficient lighting: Switching to LED and motion-sensor lighting is one of the quickest and most impactful ways to reduce energy consumption. Federal government statistics reveal that LED lights consume around 75 per cent less energy than halogen lights and last five to 10 times longer.
Renewable energy sources: Installing solar panels on the roof of your warehouse can harness the sun's natural energy, reducing reliance on non-renewable energy sources and lowering greenhouse gas emissions.
Insulation and “cool roofing”: Ensuring your warehouse is well insulated, including your roof, doors and windows, can play a big part in keeping it cool or warm without the need to rely on air conditioners or heaters.
Another sustainable warehousing idea is installing a “cool roof” in the form of roof coverings that reflect rather than absorb sunlight. Or you can opt for a “green roof” where plants or greenery are installed on your roof to help ensure warehouse temperatures are regulated.
Optimised transportation: Streamlining transportation logistics to minimise fuel consumption, emissions and vehicle idle time can contribute to greener warehouse operations.
This can include planning routes to ensure the shortest distance is travelled or using more sustainable transportation methods like electric or hybrid vehicles. You could also partner with other warehouses so you can store goods in different regions and, therefore, can deliver locally.
Eco-friendly packaging: Prioritising packaging made from biodegradable, recyclable or reusable material will not only reduce your environmental impact, but also help you appeal to customers.
Research shows that 80 per cent of Australians are influenced by packaging in their buying decisions, and 62 per cent are willing to pay more for everyday items packaged with sustainable materials.
3. Increased use of RFID technology
RFID technology explained
RFID, or radio frequency identification, is technology that uses electromagnetic fields to automatically identify and track tags attached to individual warehouse items or pallets. These tags contain electronically stored information that can be remotely retrieved using an RFID scanner.
This means that items are automatically tracked as they enter, move through and exit your warehouse. Unlike barcode scanning, which requires manually scanning each item one by one, RFID technology can automatically scan multiple items simultaneously, saving considerable time and effort for warehouse staff and eliminating human error.
How RFID enhances warehouse management
Here, we explain the four most effective ways RFID technology can be used in a warehouse to save time and dramatically improve accuracy when receiving stock, tracking inventory and dispatching orders:
Receiving stock: When a pallet of stock is received at the warehouse, the RFID scanner will automatically read the tag on the pallet. The information in the tag will then be immediately transferred to your inventory management software.
Monitoring inventory: The beauty of RFID technology is that scanners can be positioned throughout your warehouse and scan tags in any location, at any time. The information from the tags is automatically relayed to your inventory management software, which provides up-to-date visibility of your stock, allowing you to see if any items have been mistakenly removed, lost or stolen.
Stock location optimisation: With RFID technology providing up-to-date visibility on stock volumes and their location in your warehouse, you can easily work out the best location to store incoming stock.
Dispatching orders: RFID technology helps significantly boost picking and packing accuracy. An RFID scanner will ensure an outgoing pallet or order contains all the correct items before they are sent for delivery.
The benefits of RFID technology for warehouse operations
Research shows that RFID technology boosts inventory accuracy from an average of 65 per cent to more than 95 per cent. It is therefore no wonder why so many warehouses are expected to adopt the technology. Not only does it increase accuracy, but it also relieves warehouse staff of labor-intensive manual scanning during the picking and packing process.
RFID technology helps prevent inventory shrinkage and loss by enabling tighter control and monitoring of inventory movements. And it removes the risk of human error that regularly plays a factor when manually scanning items while receiving stock and dispatching orders.
4. The rise of AI-powered warehouses
The impact of AI on warehouses
Like so many other businesses and facilities, AI is fast being embedded into warehouse processes to unlock efficiencies and insights that even a few years ago would have seemed impossible.
Research shows that over a third (38 per cent) of logistics and manufacturing companies are using AI, which helps reduce operating costs in logistics by up to 50 per cent.
Advanced AI algorithms can quickly analyse vast amounts of historical or real-time data from various sources – for instance, sales, customer, supply chain or delivery data – to help warehouses ensure they have the right amount of stock on hand.
AI can also use data to deliver predictive insights that help optimise the picking and packing process, anticipate supply disruptions and trends, and deliveries.
How predictive AI is helping warehouses
Warehouses worldwide are fast adopting AI to gain a competitive edge. Let’s look at some of the ways it can provide predictive insights to optimise processes:
Anticipating demand: By analysing historical data about past orders, market trends, promotional events or even the weather, AI can predict future demand patterns and seasonality trends for certain products.
Inventory optimisation: Using insights into future demand, as well as data about lead times and supplier performance, AI helps warehouses ensure they have the right amount of stock in the right place at the right time.
Predictive picking: AI algorithms analyse order profiles, SKU characteristics, the warehouse layout and picking routes to optimise picking and packing processes.
Delivery route optimisation: By considering factors such as distance and vehicle capacity constraints, traffic conditions, delivery schedules and customer preferences, AI helps warehouses minimise travel time, fuel consumption and transportation costs while maximising on-time deliveries.
Supply chain analysis: AI can leverage historical data on past disruptions, supplier performance metrics, transportation data, weather forecasts and market trends to help warehouses anticipate supply chain disruptions.
Predictive maintenance: Equipment sensor data, maintenance records and historical failure patterns are analysed to predict equipment failures and maintenance needs before they occur.
5. The continued rise of warehouse robots
Warehouse robots are nothing new, but they are quickly becoming more advanced and effective.
From robotic arms that take away the heavy lifting from workers to robots that move autonomously between aisles picking items off shelves, automation technology is helping warehouses boost productivity, minimise errors and increase safety.
Warehouse robotic technologies explained
Warehouse robotics refers to the use of autonomous robotic systems and automation technologies to perform tasks within a warehouse or distribution center like picking, packing, sorting, transporting items and storing goods.
Robots can range from simple, autonomous machines to complex, integrated systems that work collaboratively with humans and other equipment. Some are equipped with sensors or cameras to navigate warehouse environments, interact with inventory and perform tasks with precision.
There are many kinds of robots used in today's warehouses, including:
-
Collaborative robots that work alongside and share workloads with humans.
-
Robotic arms that can pick, pack and move items with speed and precision.
-
Automated storage and retrieval systems (AS/RS) that move through aisles and retrieve items from shelves via a crane or lifter.
-
Aerial drones that fly autonomously through a warehouse to help count stock.
-
Autonomous mobile robots (AMRs) that navigate through a warehouse via sensors and onboard cameras pick items or pallets off shelves and transport them to the packaging zone.
-
Automated guided vehicles (AGVs) that can carry items along a pre-defined track, like a wire embedded in the warehouse floor.
The evolution of warehouse robots: What does 2024 have in store?
The field of robotics is constantly advancing, bringing new innovations to warehouse automation.
The global warehouse robotics market is expected to grow 16.13 percent in 2024, and as such, powerful new forms of technology are likely to be introduced to warehouses and fulfilment centres.
In years past, robots typically operated without integration with other systems or warehouse infrastructure. But we are now seeing the emergence of automation technology that is fully integrated with cloud software, other robots and the humans that work around them.
In 2022, Amazon introduced its first fully autonomous robot to its fulfilment centres called Proteus, which can move beneath mobile carts filled with packages and move them without any human control.
A similar robot, Hercules, was launched in 2023. It uses a 3D camera to navigate through a fulfilment centre to pick up mobile shelves of goods and deliver them to employee workstations. Hercules can carry loads of up to 566 kilograms and communicates with other robots and humans wearing a Wi-Fi transmitter.
In 2024, the fulfilment giant plans to launch its AI-powered robotic workcell called Cardinal that transforms manual, batch-based tasks into a seamless, automated workflow. With the help of AI and computer vision, Cardinal can identify and select a single package of up to 22 kilograms from a stack, lift and scan its label, and then place the package in an Amazon GoCart.
Another warehouse robot that Amazon is currently testing is Digit – a humanoid bipedal robot that can walk around its fulfilment centres retrieving and storing goods. This advancement is part of Amazon's new Sequoia robotics system launched in late 2023 in one of its fulfilment centres in Houston, Texas. We could see Digit rolled out to further Amazon fulfilment centres this year.
Futureproof fulfilment with Access Mintsoft
Another piece of innovative technology that is helping warehouses and fulfilment businesses automate time-consuming tasks is cloud-based warehouse management software.
Access Mintsoft is a powerful cloud-based warehouse management solution that empowers over 600 organisations worldwide to stay ahead of upcoming warehousing trends and future-proof their business.
The solution is designed by fulfilment industry experts to meet the specific needs of warehouses. Boasting over 175 pre-built integrations with leading couriers, multi-carriers and marketplaces, Access Mintsoft can integrate all your fulfilment functions in one intuitive platform while helping you process order faster and more accurately.