What is Lean Construction? Core Principles, Methods, and Benefits
Lean construction is a project management methodology with six core principles that focus on maximizing value and minimizing waste throughout all phases of the construction process. Lean construction is transforming the industry in the United States as more construction companies adopt this methodology to build faster, smarter and with higher profit margins.
In this guide, we break down the core principles of lean construction, the benefits of implementing lean practices on projects, and how to implement this approach across your construction company.
What is Lean Construction?
Lean construction is a project management methodology with the goal of completing construction projects efficiently by minimizing waste and maximizing customer value throughout all phases of a project.
This methodology incorporates an optimized workflow, a focus on waste reduction, and encourages collaboration across teams at every stage of a construction project.
In the United States, the lean construction management approach is proven to be cost-effective and results in higher margins, improves quality control, and delivers projects at a faster rate.
The origins of the lean construction methodology can be traced back to Henry Ford's assembly line approach in 1913. A few decades later, in the 1930s, Kichiro Toyoda, founder of Toyota, reimagined a more streamlined process to reduce product costs. It was in 1992 that a group formally named the construction methodology "lean construction." It has since become a standard method of completing construction projects. There are now certifications and courses offered on how to implement lean construction in projects.
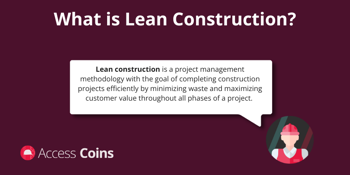
What are the Principles of Lean Construction?
The principles of lean construction are based on six core ideas that accomplish the goal of delivering a construction project efficiently to the client’s satisfaction.
The principles of lean construction are:
1. Customer Value
2. Value Stream
3. Workflow
4. Waste Reduction
5. Pull Planning
6. Continuous Improvement
Aligning the right technology platform with these principles is effective if you’re working within a centralized platform such as an Enterprise Resource Planning (ERP) system. This system provides a platform for teams to collaborate through real-time data, visibility of cash flow, and resource management throughout all phases of the construction project.
1. Customer Value
The first principle of lean is customer value. The key is to discover what the client values and what matters most to them. This will allow you to make every decision throughout the construction project with their values in mind.
For example, a client’s value can be tied to a specific budget, quality materials, safety, sustainability or design outcomes.
Failing to define value can lead to misaligned expectations or costly assumptions. Without a clear definition of customer value, the team risks overspending and prioritizing the wrong objectives.
One way to ensure the client’s value is clearly defined is by streamlining communication with stakeholders early in the construction project planning phase and ensuring every step aligns with their vision.
2. Value Stream
This principle in the lean construction methodology outlines all the steps to achieve the client’s vision from design to the completion of the construction project.
This principle is important because this process provides an opportunity to identify inefficient systems and wasteful steps that don’t add value to the lean construction methodology. A clearly defined value stream identifies bottlenecks and delays across all stages of the project.
3. Workflow
A streamlined workflow is essential to achieve the benefits of a lean construction project. This principle ensures a steady workflow is built across all teams and phases of the project. This principle emphasizes the importance of creating a continuous flow, ensuring that each phase of the construction project is ready to be worked on without disruption or delay.
Because you have identified the value and value stream, you can create a workflow that ensures a steady pace of progress is happening. This is an important principle because an interrupted workflow leads to inconsistent progress and costly downtime, resulting in high costs and inefficiencies. The goal is to keep your teams and crews productive and avoid midstream changes.
4. Waste Reduction
The next principle in lean is waste reduction. The goal of this principle is to identify the seven types of waste in construction that will lead to delays, reworks, and frustration across all teams.
The seven types of waste defined by lean construction are :
• Overproduction
• Defects
• Inventory
• Waiting
• Transportation
• Motion
• Untapped talent
For example, waste can manifest in the form of waiting for decisions, incomplete designs, inadequate communication, or materials arriving too early or too late, as well as duplicated efforts.
5. Pull Planning
Pull planning is an essential step to complete the project on time. This principle is a scheduling strategy that works collaboratively with every team and stakeholder to plan schedules and prioritize tasks that need to be completed first and efficiently.
This is important to ensure that no bottlenecks or teams are waiting for the next phase of a project. Pull planning is implemented by ensuring all teams are aware of each phase's requirements to ensure the project is completed on time.
6. Continuous Improvement
The final principle in the lean construction methodology is continuous improvement. Each workflow or project phase should be improved upon if needed. Construction companies should continually seek ways to optimize processes that are not working effectively or to identify additional methods for reducing waste and increasing efficiency.
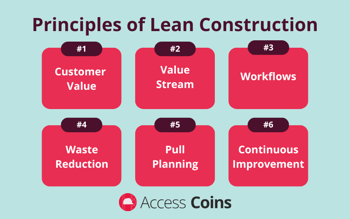
What are the Benefits of Lean Construction?
The benefits of the lean construction methodology include:
- Cost savings
- Higher profit margins
- Waste reduction
- Improved quality control
- Faster project delivery
- Satisfied clients
Growing construction companies are turning to implementing lean because it's a proven framework and strategy to deliver projects faster with minimal errors, less waste, and higher customer satisfaction.
The lean methodology enables construction companies to remain competitive, profitable, and reliable when bidding on construction jobs.
Cost Savings and Higher Profit Margins
The most impactful and appealing benefit of implementing lean construction is the cost savings and high-profit margins it offers to both the client and the construction company.
The lean construction methodology emphasizes working efficiently and eliminating waste. Often, financial loss comes from excessive materials, inefficient scheduling, wasted hours, and miscommunication.
By maximizing value and minimizing waste through improved workflows, your projects become more profitable, and you become a more appealing bidder for future construction jobs.
Waste Reduction
Waste reduction is another benefit of the lean construction methodology. Minimizing or eliminating the time, labor, and materials that don't align with the project or don't contribute value will result in fewer delays, better safety, and lower operating costs.
Improved Quality Control
Implementing lean construction leads to a more effective quality control process by emphasizing collaborative work across teams with streamlined communication.
By improving communication and strategic planning, you can strengthen coordination across teams for quality issues. By having a standard process in place, rework is minimized since everyone is on the same page. This results in fewer defects and consistently high-quality work that meets and exceeds the client's expectations.
Faster Project Delivery
By focusing on defining the customer value, value stream, and pull planning, you accelerate project timelines without compromising the quality of your work. Your team can move more efficiently from one phase of the project to the next with minimal disruptions, ensuring projects are completed on time or ahead of schedule.
Happier Clients
When a construction project is delivered on time, within budget, and built to a high standard, clients are happier. Lean construction creates this by being collaborative at every stage to ensure everyone is aligned on the end goal. Happier clients lead to an opportunity for repeat business, and a good reputation for quality work in the construction industry.
Streamline Data center construction projects with Access Coins
Access Coins supports data center construction by streamlining project management and optimizing resource usage, helping you meet the evolving demands of modern infrastructure while staying within budget and regulatory requirements.
How to Implement Lean Construction
Implementing lean construction is more than adjusting a workflow or improving communication among your teams. It’s a cultural and operational shift across all teams and areas of the company and requires you to rethink how you plan and build projects.
To implement lean construction, you need to:
- Train your project teams
- Introduce lean in phases
- Introduce a ‘Change Agent’
- Test lean on pilot projects
- Use a construction ERP to support lean practices
Train your Project Teams
Implementing lean is a culture change to ensure your team has the training and knowledge to understand lean and the benefits it brings. To implement lean construction, you must train your project teams to understand the tools, terminology, and mindset associated with lean construction.
Training your project teams should focus on the principles and benefits of lean, as well as what that actually looks like across teams, roles and construction sites. When your teams understand lean and why it works, it leads to more effective collaboration.
Introduce Lean in Phases
Lean is a significant change, and it will need to be introduced in phases across your team rather than implemented all at once. A large rollout without proper planning can overwhelm teams and result in poor adoption across the organization.
Introduce lean in phases for smaller and manageable changes to allow teams to adapt and view early wins. Start with specific processes or teams, one at a time, across the organization and company.
Introduce a ‘Change Agent’
Introduce a change agent, who is a leader who ‘makes things happen,’ and champions lean across the business. Your change agent must be resilient in championing lean in case of any friction or resistance to the change.
A strong agent ensures that lean is a priority and doesn't get derailed by old habits. This change agent drives the transition to lean, educates others across teams, and maintains momentum throughout the implementation of lean from start to finish.
Test Lean on Pilot Projects
Test lean on pilot projects before implementing lean across the company. By piloting lean on one or two test projects, you can identify weak spots and learn where to begin improving the rollout of lean throughout the company.
A test project enables teams to work through lean principles in controlled environments with a hands-on approach, identifying gaps and challenges early on before implementing them company-wide. This will help teams and key stakeholders to view and understand the impact and benefits of lean.
Use Construction ERP to Power Lean
For lean construction to function effectively, real-time information, collaboration, transparency, and coordination are essential. Construction ERP software is a digital system that enables teams to work from the same source of truth across construction data.
A construction ERP system will help streamline procurement, align schedules, and tasks across all phases of the construction project. Construction ERP software enables lean practices, reduces downtime through better resource planning, and gives greater visibility into the construction project.
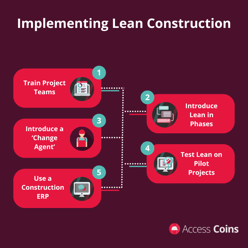
Power Lean Construction with Access Coins ERP
Access Coins is an ERP system developed specifically for construction.
It helps power lean construction methodology through:
• Real-time data collection
• Building automated workflows across your teams
• Ensuring your teams are on the same page
• Tracking all costs and cashflow
• Reducing waste through automation