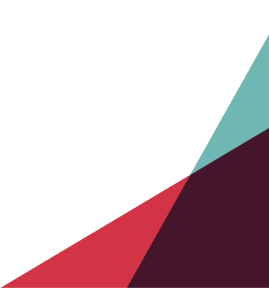
What Is the Best Manufacturing Production Scheduling Software?
Read our essential guide on the best production planning software – and discover which system will work best for your manufacturing business.
Written by Rod Schregardus
What Is Manufacturing Production Scheduling Software?
Between allocating resources, planning capacity, minimising work in progress (WIP) and minimising lead times, there’s a lot of moving parts for manufacturing managers to keep an eye on.
Manufacturing production scheduling software is designed to streamline operations and make life easier for those in charge. It gives team leaders a real-time view of their labour, equipment and materials, allowing them to see where resources are being used efficiently and where certain functions are underutilised or overburdened.
Efficiency is king in manufacturing, and industry leaders are constantly optimising their processes wherever possible. Businesses that integrate the best production scheduling software for their specific needs are more likely to gain a competitive edge and enjoy a range of benefits, including:
- Higher productivity – Smoother production flows and reduced idle time can have a big impact on site performance.
- Cost savings – Effective scheduling allows managers to optimise resources, reduce inventory carrying costs and cut overtime expenses.
- Shorter lead times – Having a 360-degree view of production can help managers to reduce the time it takes to source materials, manufacture goods and deliver finished products.
- Less downtime – The right software can flag up scheduling conflicts and bottlenecks, leading to fewer machine breakdowns and maintenance issues.
- Better decision-making – Intuitive data dashboards make it far more simple to get a handle on analytics, and spot recurring trends and insights that can inform key decisions.
Every type of manufacturer could gain by integrating a production scheduling software, from small-batch manufacturers and MTOs, right through to high-volume and mixed-model operations.
Of course, needs differ from business to business, which is why it’s essential to plan ahead and conduct detailed research to identify the best manufacturing production scheduling software to suit your main objectives.
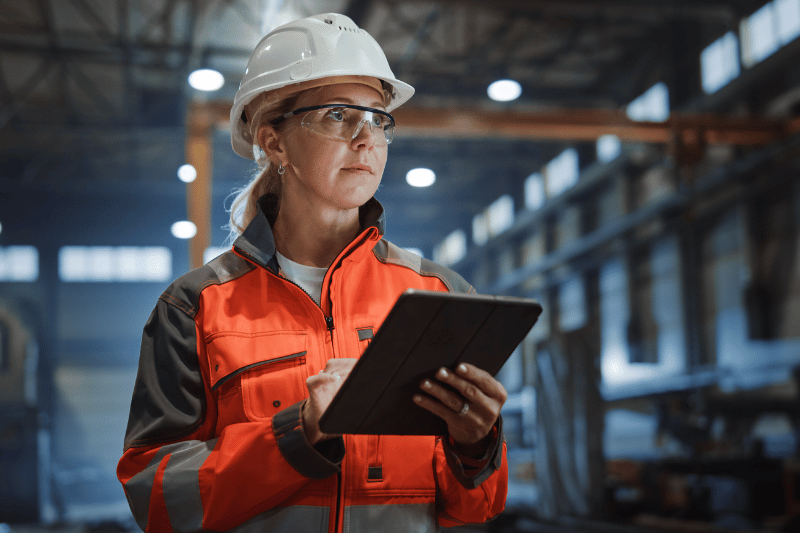
What Are the Key Features of a Manufacturing Production Scheduling Software?
Day-To-Day Scheduling
Keeping all schedules and systems running like clockwork is perhaps the biggest challenge that manufacturing production managers face on a daily basis. A production scheduling system underpins operations by tracking work orders and prioritising operations in the right sequence – always within clearly scheduled timeframes.
This helps managers avoid excessive wait times and manage sudden changes whenever there is a rush order, a breakdown or material shortage.
Capacity Planning
Production managers used to spend days maintaining complex spreadsheets in order to plan resources and monitor capacity constraints. Even then, human error could often creep in, leading to inefficient planning and operational performance.
Today’s best manufacturing production scheduling software helps managers distribute production in the most efficient way across available resources. Systems automatically take into account the capacity limitations of staff and equipment, which reduces the risk of machinery bottlenecks and production delays.
‘What-If’ Analysis and Forecasting
By using software to predict ‘what-if’ scenarios, production managers can forecast the impact of fluctuations in demand or drop-offs in resource availability. For instance, if supply chain disruption leads to a shortage of materials then how badly would this impact production and which resources could be redeployed to other areas.
‘What-if’ analysis is also a useful capability if businesses are looking at expanding their operation. It gives them a clearer idea of the challenges and constraints that would come with an increase in production, as well as the business functions that would require more attention and investment to keep up with the new scale of operations.
Real-Time Insights
Manufacturing production leaders need to be able to check in on every corner of their operations at any given time. Intuitive dashboards that provide real-time visibility are invaluable in this respect, whether it’s tracking the status of an order or getting an instant rundown of inventory levels.
Linking back to capacity planning, one feature that greatly benefits managers is receiving instant notifications whenever materials are running low or machinery requires maintenance, giving teams more time to plan a resolution and avoid downtime.
Just-In-Time (JiT) Scheduling
Producing products precisely when they are needed comes with a unique set of challenges. Manufacturers that specialise in ‘just-in-time’ scheduling need to be meticulous in their approach to resource allocation and material planning, as well as being agile enough to respond to sudden order changes on the fly.
Predictive analytics can be a big help to JiT manufacturers by pulling historical data and market trends to anticipate future demand and potential scheduling requirements.
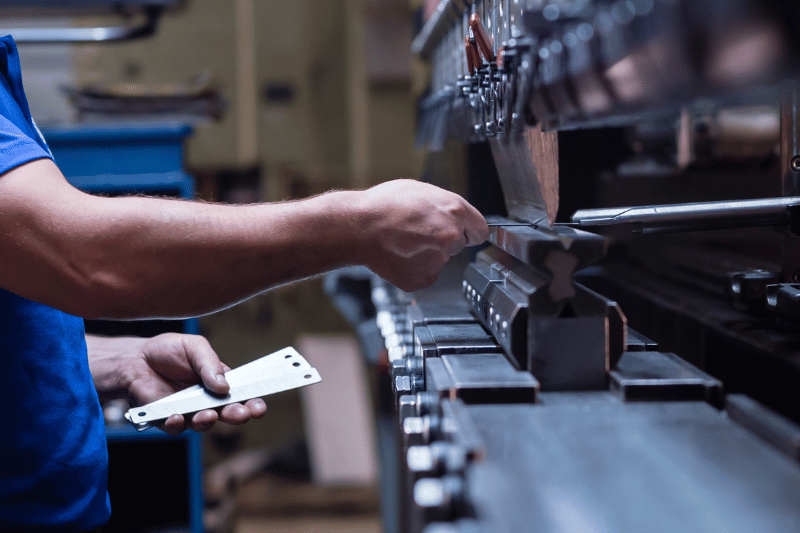
The Best Manufacturing Production Scheduling Software to use in 2024
Not all manufacturing production scheduling systems are created equal. Some prioritise flexibility, customisation and user experience, whereas others offer a stronger analytics function, or seamless integration with an existing tech stack.
We’ve examined four of the most popular platforms used by manufacturing companies in the UK to give you a fair assessment of their similarities and differences in capability – and to help you decide the best fit for your business.
Simio
Simio is a manufacturing production planning software that specialises in simulation models and risk analysis. This is a good option for companies that want to build detailed schedules that predict and plan for all eventualities, while conducting risk analysis in real time. There is also a free version of the software available, although the features are relatively limited.
Key features
- Simulation models
- Risk-based scheduling
- 3D object-based modelling
- Data visualisation and reporting
PROS |
CONS |
The basic version is free to use |
Limited features with free version |
Good for risk-based scenario planning |
Advanced capabilities aren’t user-friendly |
Helps to solve scheduling dilemmas |
Users report bugs and lags |
Monday.com
Monday is a flexible, all-purpose platform that is used by thousands of businesses worldwide. Although it is not specifically designed for manufacturing purposes, the user experience and ability to integrate with other systems still make it a popular choice.
Key features
- Automate workflows
- Track production processes
- Capture orders and customer requests
- Report on delivery times and pipeline status
PROS |
CONS |
Lots of integrations with other software |
Not specifically designed for manufacturing |
Great tracking features and visual boards |
Tiered ‘per-user’ pricing can be limiting |
Variety of templates to match user needs |
Doesn’t offer advanced scheduling abilities |
Siemens Opcenter
Opcenter is an advanced planning and scheduling software (APS) that uses advanced algorithms to balance capacity and demand, and generate efficient production schedules. The system enables increased resource utilisation and on-time delivery, while also helping to reduce inventory levels and waste.
Rather than an all-in-one platform, Opcenter is split into several different software packages that cater to specific needs and functionalities.
Key features
- BOM-level planning
- Advanced constraint modelling
- Schedule optimisation
- Assembly process visualisation
PROS |
CONS |
Designed to meet manufacturing needs |
Not easy to integrate with other software |
End-to-end visibility of production |
Lack of in-built interactive dashboard |
Large reseller network |
Not multi-user |
Access Orchestrate
Access Orchestrate is an intuitive production planning and scheduling software designed with the demands of manufacturing companies in mind. The platform ensures that users are utilising every machine, employee and resource to its full capacity. It gives users a clear view of schedules and statuses at all times, and easily integrates with other systems.
The cloud-based software can be deployed to support sites of all sizes. It’s part of the Access Workspace suite of products, offering seamless connectivity with other core business functions.
Key features
- Advanced planning and scheduling capabilities
- End-to-end visibility of capacity and resources
- ‘What-if’ scenario-based planning
- Real-time dashboards to track production
PROS |
CONS |
Designed to meet manufacturing needs |
No free version |
Easy integration with MRP/ERP systems |
Cost could be an issue for smaller companies |
Multi-user functionality available as standard |
Bespoke customisation of the product not available |
Microsoft Excel
Although now considered a legacy system by industry standards, Excel remains a popular choice among manufacturing businesses that haven’t yet made the shift to a specialised production scheduling software.
There’s a reason why businesses have been using Excel for production planning and inventory management for over 40 years. It has long been the most readily available, low-cost option on the market, allowing users to build schedules using spreadsheets and downloadable templates.
Key features
- Ready-to-use templates for scheduling
- Little training needed to start
- Intuitive calculation functions
- Built for smaller businesses with less complex needs
PROS |
CONS |
Affordability |
Spreadsheets take days to build |
Widely available support materials |
Manual data entry prone to human error |
Can be integrated with other systems |
Version control an issue with multiple users |
ERP Systems
Enterprise resource planning systems (ERP) ensure that business processes like materials planning, forecasting and sales order processing all work seamlessly together from a single source of data. Data analytics gained through an ERP platform can directly inform decisions at management and board level, offering real time insights into operations and highlighting any areas that require additional focus.
ERPs are often used in tandem with advanced planning and scheduling systems (APS), funnelling the data to run algorithms that provide the many outputs for scheduling. An APS then uses that information to create a production schedule for every manufacturing cell or line based on the constraints of a specific operational set up.
Key features
- Integrated modules
- Centralised database
- Workflow automation
- Reporting and analytics
PROS |
CONS |
Streamlines business processes |
Usually need to be paired with an APS |
Better resource management |
Charts can be difficult to configure |
Can be integrated with other systems |
Lack of scenario analysis |
Why choose Access Orchestrate production planning software?
Access Orchestrate production planning software for manufacturing ensures that you are utilising every machine, employee and resource to its full capacity.
Manufacturing scheduling software allows production plans to be changed quickly and easily. Planners can analyse capacity, test different scenarios to answer ‘what if’ questions and identify issues before they occur.
Our production scheduling software saves time, reduces waste and prevents errors, while improving communication between teams.