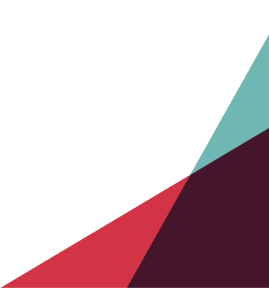
What is a Material Requirement Planning (MRP) System?
Material requirements planning (MRP) systems offer cost-effective, scalable, often cloud-based solutions that deliver greater control and effective manufacturing production management.
There are different elements to MRP, including estimates and quotations, purchasing, stock control and production costs management, and, when combined with additional finance and accounting functions, provide complete visibility from quote to invoice.
Written by Ben Hulland
Key features of an MRP system:
- Shop floor data collection and job costing: analyse time spent on production with touchscreens at workstations to track:
- Machine downtime
- Unproductive working hours and scrap levels
- Real-time measurement of OEE
- Document and information management: Product drawings, images, and training information are available to staff and supervisors so that everything the team needs to do their job is at hand.
- Purchasing and supplier management: automatically raise POs, track deliveries, and manage invoices.
- Traceability for QA: Provide full traceability of every material and component throughout the manufacturing process.
MRP systems support a wide range of manufacturing sectors including pharmaceutical, aerospace, automotive, metal fabrication, precision engineering, and food and drink.
What are the benefits of an MRP system?
An efficient MRP system simplifies processes and planning. Modular MRP software can save time, increase productivity, and reduce costs.
1. Gain Visibility
With your operational data and processes in one system, MRP software delivers visibility from quote to invoice.
2. Control Your Cashflow
MRP can help limit the amount of cash tied up in stock, ensure on-time delivery to customers and better control on margins with increased quote accuracy.
3. Increase Productivity
MRP systems significantly increase worker productivity; with manufacturing data available in real-time digitally, workers have instant access to relevant information.
4. Save Time on Administration and Repetitive Tasks
Automating often manual, paper-based and spreadsheet-based processes speeds up decision-making and reduces errors.
5. Transform Quality Management
The best MRP systems guide manufacturers through the process of conforming to strict quality accreditations. Identifying errors is simpler in case of quality issues or non-conformances.
6. Improve Relationships with Customers and Suppliers
MRP allows businesses to manage stock and materials more effectively, ensuring customers consistently receive products that meet their needs and are of high quality, and that suppliers have clarity on what’s needed when.
7. Better informed decision-making
Easily compile and analyse data - MRP systems allow businesses to set up and monitor specific KPIs and productivity.
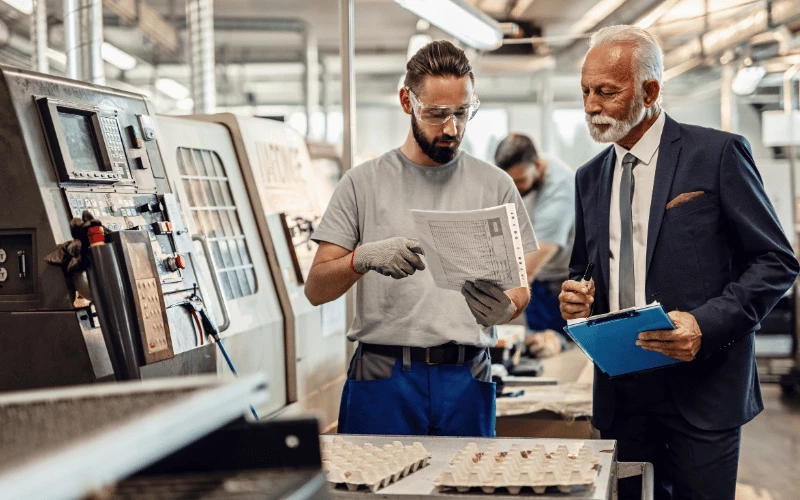
How does an MRP system work?
MRP enables manufacturing businesses to run every stage of their operations more efficiently, areas such as stock, purchasing, quality and sales orders, by offering a single source of truth. Shop floor data capture and integration with finance systems brings in an additional layer of data for a complete view of manufacturing operations.
MRP systems help businesses:
- Accurately define what needs to be produced and describe the order in which the material will be required.
- Quantify the demand and calculate the required quantity for final products to meet demand.
- Determine the supply and calculate the assemblies, components, and materials that must be produced or purchased over the planning period.
MRP transforms how information is stored and accessed, delivering real-time insights and the opportunity for in-depth analysis.
What do MRP I and MRP II Mean?
These terms explain the evolution of MRP – MRP I and MRP II are the descriptions for very early systems.
MRP was introduced in the 1960s, and thousands of businesses worldwide rapidly adopted the software. MRP software allowed businesses to significantly increase production speed and save money by accurately estimating material requirements.
The first MRP system is referred to as MRP I, and it allowed businesses to obtain information about customer demand and the bill of materials for the finished product, which could then be used to calculate material requirements and develop purchasing plans and production schedules.
However, while helpful, MRP I answered only some of the questions manufacturers had about their operation, so MRP II emerged in 1983 as an evolution of MRP I. The focus for MRP II was broader Manufacturing Resource Planning. MRP II accounts for other aspects of the manufacturing process, such as capacity planning, shop floor control, purchasing management and stock control. MRP II has additional inputs such as resource schedules and sales order processing. This means that the outputs are much more accurate, allowing manufacturers to define how long it takes to produce products more precisely.
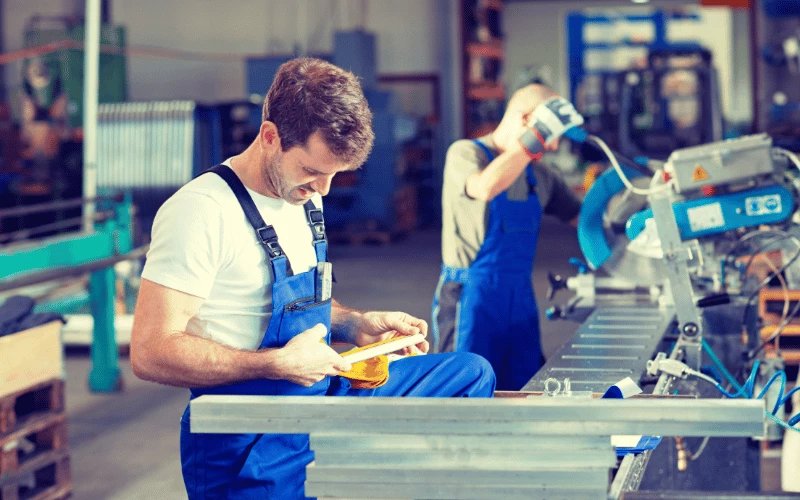
What is the difference between MRP and ERP systems?
MRP focuses solely on the manufacturing-centric processes of a business. In contrast, ERP offers greater functionality across a whole business; MRP may be one specific module within an ERP system.
ERP is a centralised system helping organisations integrate, automate, and manage critical business processes, such as sales, HR, finance, CRM, manufacturing, and supply chains. These processes work together to drive the business. ERPs are helpful for any business in any industry, although it is more often used by large organisations.
SMEs are more likely to have an ERP ‘system’ consisting of an MRP with separate or integrated software covering finance, CRM and so on, incorporating more as required as the organisation grows. This set up offers a flexible, scalable solution with many of the benefits of ERP.
Choosing between MRP or ERP is a decision very much dependent on the specific needs of a business, and sometimes, the budget available.
Where manufacturing process control is a critical business requirement, then MRP may be the right solution for you.
ERP is more relevant for an organisation needing to bring together broader business functions.
Learn about the differences between ERP and MRP by going to our article: ERP or MRP - All You Need to Know >
How to Implement an MRP system:
The smooth implementation of a new MRP system is vital to minimising disruption for your business and to ensuring you are getting value from your investment as quickly and as fully as possible.
MRP software providers should be on hand to guide and support you and your teams through the process and beyond. At each phase, progress should be tracked and communicated in collaboration with your supplier.
- Getting started - there should be a clear plan of action for the implementation, with information on roles and responsibilities and in-depth product demos for key project team members
- Preparation - existing system will need to be configured ahead of launch
- Training for all relevant teams
- Validation – testing and checks to ensure systems are working as expected
- Launch
- Review – assess progress and any issues
Once your chosen MRP package has been successfully implemented, it’s important to ensure that there is access to further support if needed and dedicated teams who can quickly solve any day-to-day problems should they arise.
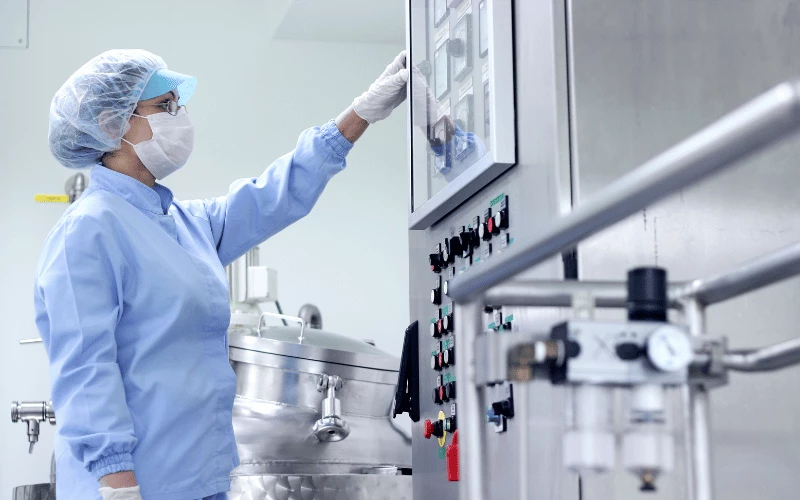
How to choose the right MRP System:
Choosing MRP software can be daunting, there are many options to choose from; there are some which are more suitable for specific industries, and some which are more suitable to the size of your business.
Key things to think about:
- Scoping – set key objectives, appoint project manager and sponsor, agree budget, compile a list of initial requirements
- Current state – what issues are you having now? What is the business strategy one, three, five years from now? Which systems / integrations are currently in place?
- Stakeholders – map out stakeholders and collect their input – what are their needs?
- Research – ask for recommendations internally and externally, search trusted websites for options and reviews, look for case studies, use industry social media, messageboards and forums
- Shortlisting – produce a more detailed list of requirements and categorise into ‘must have’ and ‘nice to have’, and weight each of these. These could include:
- Is the software cloud-based or on-premise?
- Can the system scale as my business grows?
- Do they have implementation pathways i.e. how is the implementation managed?
- What customer support services are available?
- Does the supplier understand my industry? Do they have a track record of supporting businesses like yours? Can they provide reference sites you can speak to?
- What integrations are available?
- What support is provided before, during and after the implementation?
- How will the software be installed and configured?
- What training is provided for your teams?
Ensuring you select the right system for your business is critical – an MRP system will become a core part of your business. Careful thought and planning from the start is key.
Why choose the Access FactoryMaster MRP system?
With our cloud-based MRP system, you can import your sales orders and automatically generate purchase orders for raw material or components. FactoryMaster takes into account variables such as purchase orders, work in progress, delivery commitments, stock levels and purchase lead times.
It gives you full visibility of your operation (including shopfloor data capture) and unbeatable traceability, giving you control over your cashflow and opportunity for growth.
Explore more MRP resources and guides
MRP FAQs
What does MRP stand for?
MRP stands for, Material Requirements Planning